Magnesium Parts Are Typically Attached Using: A Comprehensive Guide For Enthusiasts
When it comes to magnesium parts, they’re often used in high-performance applications, and knowing how they're attached is crucial for anyone in the industry. Magnesium parts are typically attached using a variety of methods, from welding to fasteners, each with its own advantages and challenges. Whether you’re an engineer, a hobbyist, or just curious about the mechanics behind these parts, this article will break it all down for you.
Let’s face it, magnesium parts are not your everyday materials. They’re lightweight, super strong, and perfect for applications where weight reduction is key. But how do you actually connect them without compromising their integrity? That’s the million-dollar question we’re diving into today.
As we explore the world of magnesium part attachment, we’ll uncover the most popular methods, delve into the science behind why they work, and touch on some common pitfalls to avoid. So grab a coffee, get comfy, and let’s dig into the nitty-gritty of magnesium parts attachment.
Read also:General Labor Jobs In Detroit Mi Your Ultimate Guide To Finding The Right Fit
Understanding Magnesium Parts and Their Importance
Why Magnesium Parts Are So Special
Magnesium parts are kinda like the superheroes of the material world. They’re super light, yet insanely strong. This makes them a go-to choice for industries like aerospace, automotive, and even consumer electronics. But here’s the kicker—they’re also highly reactive, which means attaching them isn’t as simple as slapping on a couple of bolts.
Let’s take a step back and understand why magnesium is such a big deal. It’s about 3/4ths lighter than steel and even beats aluminum in the weight department. That’s why you’ll find magnesium parts in everything from jet engines to your favorite gaming laptop. But with great power comes great responsibility, and attaching these parts requires a solid understanding of the material’s properties.
Magnesium Parts Are Typically Attached Using Welding
Welding: The Go-To Method for Strong Bonds
Welding magnesium parts is like performing surgery—it needs precision and skill. There are a few welding techniques that work well with magnesium, including TIG (Tungsten Inert Gas) and laser welding. These methods create strong, reliable bonds that can withstand the test of time.
Here’s the thing about welding magnesium, though—it’s not without its challenges. Magnesium is highly reactive, meaning it loves to oxidize when exposed to air. This can lead to some pretty nasty defects if you’re not careful. That’s why shielding gases like argon are often used during the welding process to keep the material happy and prevent oxidation.
Some key welding tips for magnesium parts:
- Use clean, high-quality materials to avoid contamination.
- Ensure proper ventilation to keep the work area safe.
- Practice makes perfect—welding magnesium is an art that takes time to master.
Fasteners: Another Way to Attach Magnesium Parts
When Screws and Bolts Do the Trick
Sometimes, welding just isn’t the answer. Enter fasteners—those trusty little guys that hold things together without all the fuss of welding. Fasteners like screws, bolts, and rivets can be used to attach magnesium parts, especially when you want a removable connection.
Read also:Jared From Subway Release Date The Inside Scoop Youve Been Waiting For
Using fasteners with magnesium parts requires a bit of thought. Since magnesium is so reactive, you’ll want to choose fasteners made from compatible materials like titanium or stainless steel. Mixing metals can lead to galvanic corrosion, which is like a slow-moving disaster for your parts.
Adhesives: The Silent Heroes of Magnesium Attachment
Why Adhesives Are Gaining Popularity
Adhesives are like the quiet achievers in the world of magnesium attachment. They’re not as flashy as welding or as straightforward as fasteners, but they get the job done. Adhesives can provide strong, lightweight bonds that are perfect for certain applications.
One of the biggest advantages of adhesives is their ability to distribute stress evenly across the bond. This can help prevent stress concentrations that might lead to failure. Plus, they’re great for attaching magnesium parts to other materials, like composites or plastics.
However, adhesives aren’t without their drawbacks. They can be sensitive to temperature changes and may require special curing processes. It’s important to choose the right adhesive for your specific application and follow the manufacturer’s instructions to the letter.
Understanding the Science Behind Magnesium Attachment
The Chemistry of Magnesium and Its Impact on Attachment
Magnesium is a fascinating material, but its chemical properties can make attachment a bit tricky. As we’ve mentioned, magnesium is highly reactive, which means it loves to form oxides when exposed to air. This can interfere with the attachment process, especially when welding or using adhesives.
To combat this, manufacturers often use surface treatments like anodizing or coating to protect the magnesium parts. These treatments create a barrier that prevents oxidation and improves the bond strength of the attachment method.
Common Mistakes to Avoid When Attaching Magnesium Parts
Don’t Let These Pitfalls Trip You Up
Attaching magnesium parts isn’t rocket science, but there are a few common mistakes that can trip you up. Here are a few to watch out for:
- Not cleaning the parts properly before attachment—dirt and debris can weaken the bond.
- Using incompatible materials for fasteners or adhesives—this can lead to galvanic corrosion.
- Ignoring the importance of shielding gases during welding—oxidation is a real deal-breaker.
By avoiding these pitfalls, you can ensure that your magnesium parts are attached securely and reliably, ready to perform in even the toughest conditions.
Industry Applications of Magnesium Parts
Where You’ll Find Magnesium Parts in Action
Magnesium parts are everywhere, from the skies to the streets. In the aerospace industry, magnesium is used in everything from jet engine components to aircraft interiors. Its lightweight properties make it perfect for reducing fuel consumption and improving performance.
In the automotive world, magnesium parts are becoming increasingly popular as manufacturers look for ways to reduce vehicle weight without sacrificing strength. You’ll find magnesium in everything from steering wheels to engine components.
Even in consumer electronics, magnesium is making waves. Laptop casings, smartphone frames, and other electronic components are often made from magnesium due to its lightweight and durable nature.
Future Trends in Magnesium Attachment
What’s Next for Magnesium Parts?
The future of magnesium attachment is exciting. As technology advances, we’re seeing new methods and materials being developed to improve the process. For example, researchers are exploring the use of advanced coatings and surface treatments to enhance the bond strength of magnesium parts.
Additionally, the rise of 3D printing is opening up new possibilities for magnesium parts. With 3D printing, manufacturers can create complex geometries that would be impossible with traditional manufacturing methods. This could revolutionize the way we design and attach magnesium parts in the future.
Conclusion: Magnesium Parts Are Here to Stay
So there you have it—a comprehensive guide to attaching magnesium parts. Whether you’re using welding, fasteners, or adhesives, there’s a method out there that will work for your application. Just remember to keep an eye on those reactive properties and avoid common pitfalls, and you’ll be good to go.
Now it’s your turn. Have you worked with magnesium parts before? What attachment methods have you used, and how did they work out for you? Drop a comment below and let us know. And if you found this article helpful, don’t forget to share it with your friends and colleagues. Together, let’s keep the magnesium revolution rolling!
Table of Contents
- Understanding Magnesium Parts and Their Importance
- Magnesium Parts Are Typically Attached Using Welding
- Fasteners: Another Way to Attach Magnesium Parts
- Adhesives: The Silent Heroes of Magnesium Attachment
- Understanding the Science Behind Magnesium Attachment
- Common Mistakes to Avoid When Attaching Magnesium Parts
- Industry Applications of Magnesium Parts
- Future Trends in Magnesium Attachment
- Conclusion: Magnesium Parts Are Here to Stay

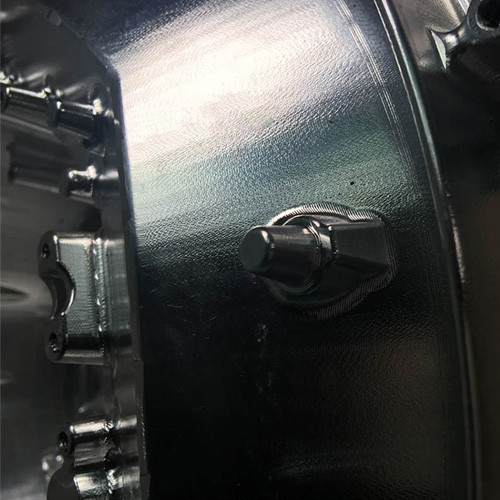
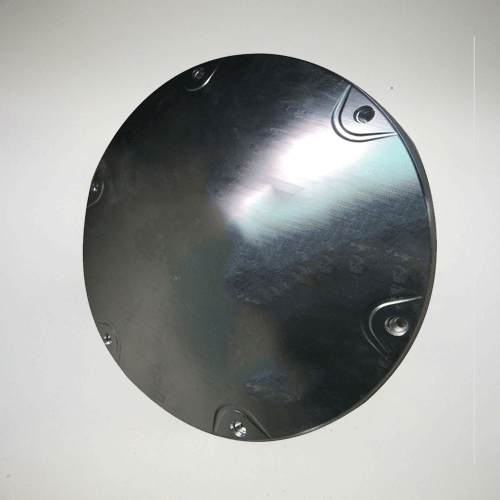